こんにちは.Maquinistaで機械班をやっていた20-Samejimaです.
皆さんはロボットを台車で運ぶ時,ロボットがガタガタ振動してしまうという経験はありますか?(ロボットに限らず,台車を使うと載せているものが振動するという経験は皆さんお持ちだと思います.)そんなロボット運搬時の振動問題について,ロボコンの裏で取り組んだのが,今回ご紹介する「除振台車」です.
除振台車プロジェクト発端の経緯
私たちMaquinistaは,ロボコンに向けて日々ロボット製作を行っています.
そんな中で,改善したいねとよく言われていたのが,運搬時の振動でロボットのねじがすぐ緩んでしまうことでした.Maquinistaには常設フィールドが無く,作業場から離れた体育館で動作確認など練習を行っています.そのため,作業場と体育館の間でロボットを台車の上に載せて運ぶのですが,その時の振動でねじが緩んで,練習でパーツが外れるなどの不具合がよく起こっていました.もちろん,気が付いたら修復すればよいのですが,奥まった所だったり少し分解ないといけなかったりすると,時間がかかってしまいます.
また,単純に,構造的に弱いパーツがキシキシ言ったり,段差や点字ブロックなどの凹凸を通るときに衝撃がロボットに加わったりと,普通の台車はロボットの寿命を縮めにかかってきますロボットにとって良くない力を伝えてしまいます.
かといって,市販されている除振台車を購入しようとすると,かなりお高くついてお財布が厳しい.
以上のような問題がチームの中で言われていたので,その解決策として,振動しない台車を作ろう,ということが2022年秋に決まりました.そして長い除振台車プロジェクトが始まったのです.
目標
ねじが緩まないようにする,衝撃を吸収するという抽象的な目標よりも,数値的な目標の方が設計しやすかったりします.そこで,10Hz以上の振動を減衰させる台車という目標を立てました.
(ねじが何Hzで緩むかはわからなかったので,10Hzという数字は勘です.)
寸法や最大積載重量も,運搬途中のエレベーターに入る大きさだったり,ロボットの重さに耐えられるように決めました.
アイデア出し
まずはアイデア出しです.なるべくお金をかけずに除振台車を作るというコンセプトをもとに,フレームなどは部室にある材料で作り,キャスターは既製品を改造するという方針で行きました.キャスターは量産効果で安くなっていて,一から自分で作るよりも安上がりなので.
まずは,どのように振動を吸収するのか考えました.例えば,振動吸収機構の取付場所も,キャスターに内蔵,台車の台の上に取り付け といったアイデアがあります.さらに,キャスターに内蔵するとしても,車輪が直線的に上下するようにするのか,軸を中心にして円弧上に上下するようにするのかなど,いろいろ考えることがあります.(↓考えた案の一部)
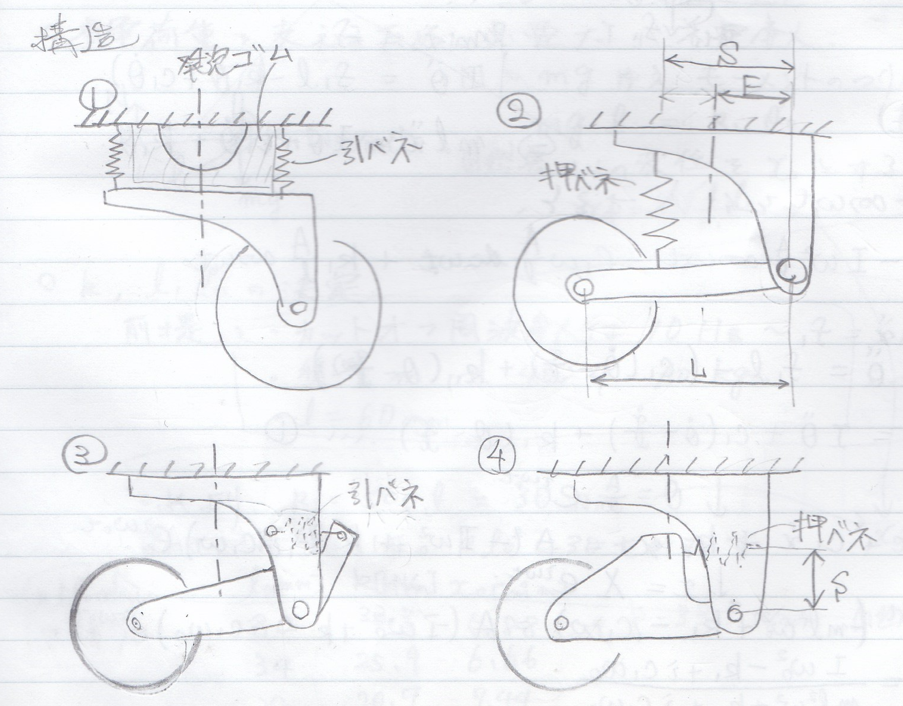
軽く実験してみたり,作りやすさを考えたり,既製品の構造を想像したりして,とりあえず上の写真の②で試作品を作ってみることにしました.
1号機製作
当然ですが今まで台車を作ったことがなく,どんなところが難しいのかわからなかったので,とりあえずの試作品として1号機(ロボット風のネーミングです)を作ってみました.実験的な意味が強いので,余った木材をテキトーに組み立てて作ってあります.
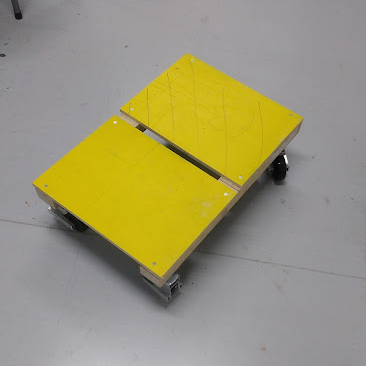
キャスター部分も下の写真でお見せします.もともとは左側のただのキャスター(これ)ですが,それを改造しました.黄色い部品がばねです.
赤矢印が書いてある方向に車輪が上下することによって,振動を吸収します(青丸印がその回転軸).
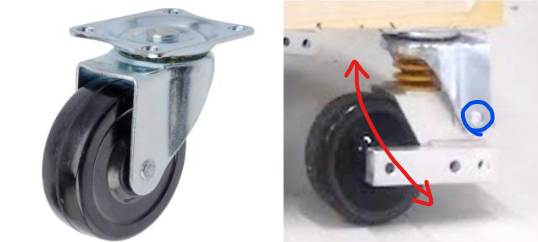
さあ,作ってみた1号機を実際の路面で走らせてみました.ちゃんと振動を吸収してる!と感じると同時に,いろいろ問題が見つかりました.
例えば,ばねの位置です.今回の位置だと,タイヤが上下したときにばねが台座からずれてしまうことがありました(青丸の回転軸からばねの端までの距離が,上端と下端で違うため).これではその都度その都度修理しなければいけないので,手間がかかってしまいます.
他にも,ストッパーが無かったので,持ち運びの時などに向きを変えると除振の機構が飛び出して,扱いずらいこともありました(↓こんな感じ(向きが分かりづらくてすいません,台車を立てかけたときのキャスターの様子です)).
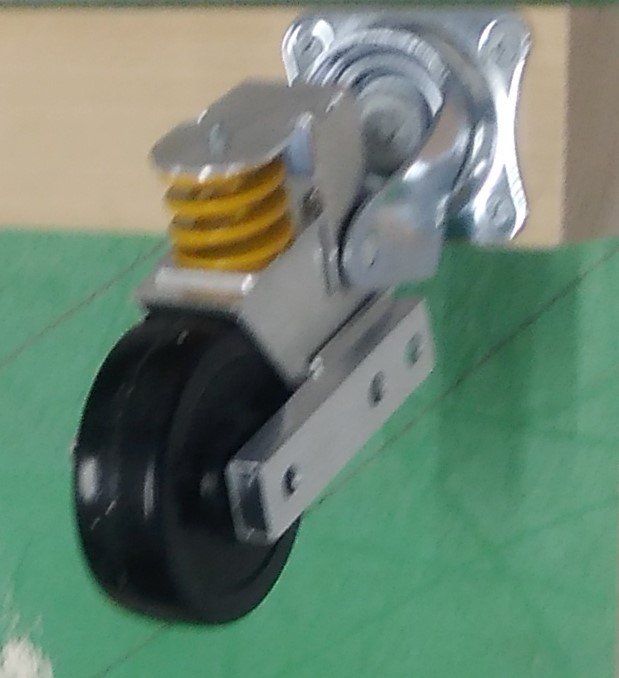
台車は使っていない時間も長いので,しまうときにも扱いやすいようにしないとダメでしたね.
他にもいろいろ問題点はあったのですが,これらをもとに2号機の設計に取り掛かりました.
2号機設計~ばねの位置について~
1号機(試作品)では,アイデアの②にあるような機構で作りましたが,これに起因する問題があるということが分かりました.そこで,この問題を解決できそうな④を選んで,設計することにしました.
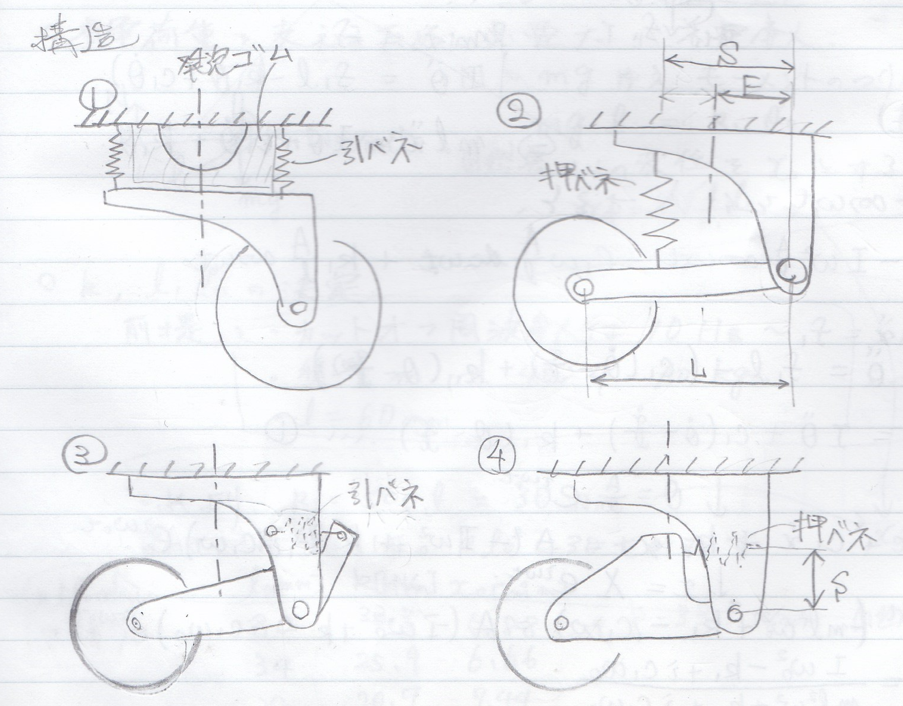
2号機設計~振動を吸収する設計~
さて,振動を吸収する設計には何が必要でしょうか.
そのカギは,振動を吸収する機構に使われているばねの柔らかさ(ばね定数)にあります.ちょっと難しいので,細かい話はしないですが,ばねは柔らかいとたくさん振動を吸収し,ばねが硬いと振動を少ししか吸収しません.ただ,ばねが柔らかすぎても台車の重さを支えきれないので,ちょうどいい柔らかさを探す必要があります.その柔らかさを計算で求めました.大学の授業でやった内容を思い出しながら…↓
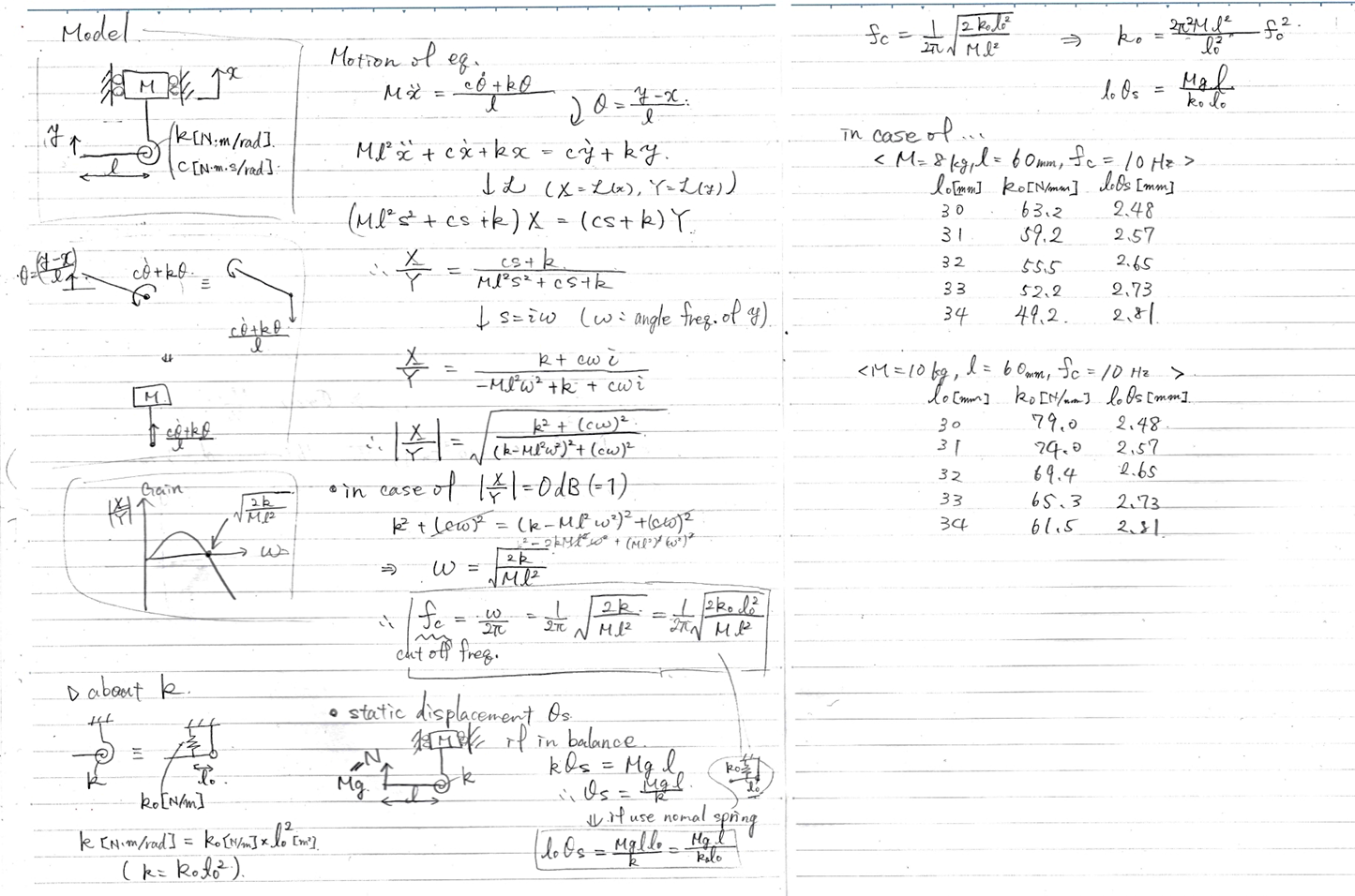
(計算の中身が知りたい人へ難しい話)←読み飛ばしてOKです!
この除振台車の数値的な目標である「10Hz以上の振動を減衰させる」を達成するばね定数を求めるために,学部2年で習う機械力学の知識を使いました.今回やったことは,簡単に言うと,1自由度基礎励振系のモデルを作り,ばね上の振動(出力)がばね下の振幅(入力)よりも小さくなる瞬間の周波数(カットオフ周波数)を計算し,その値が10Hzになるようなばね定数を計算したという流れです.
2号機設計~CADを作る~
ばねの設計だけでなく,パーツの強度計算などもやり,CADを作りました(実際には同時並行でやりました).既製品のパーツは現物の寸法を測りながらモデリングしていきます.
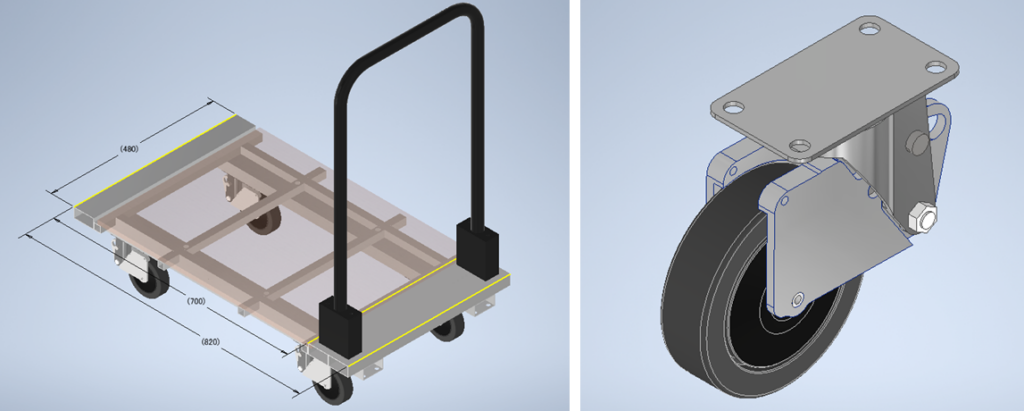
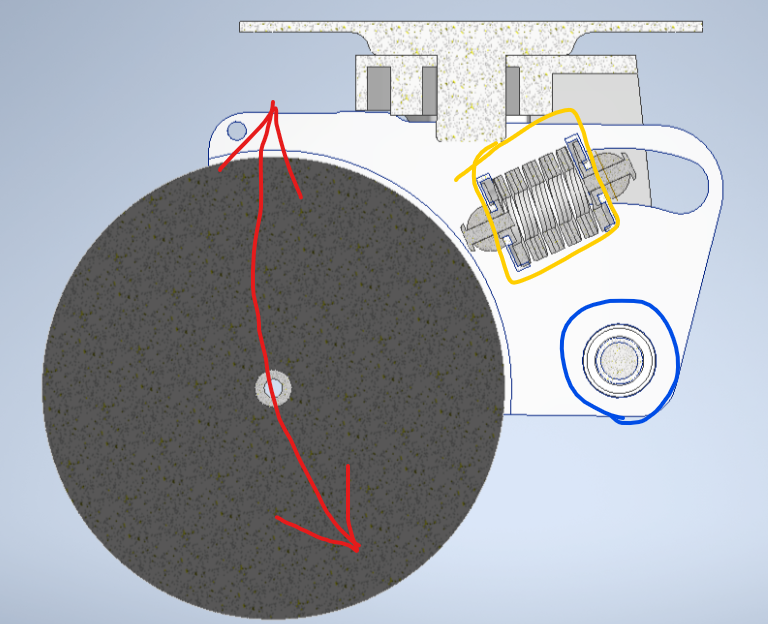
青丸の軸を中心として赤矢印の方向にタイヤが上下,黄色い四角で囲んだばねが伸び縮みすることで振動を吸収(この図は縮んだ状態)
2号機の製作
設計が終わったら,製作に移ります.アルミ板の削り出し(CNC)やアルミ角材の穴あけなどは,ロボコンと同じような材料なので,比較的スムーズにできましたが,大変だったのは振動吸収用のばねを支えるステンレス軸でした.ステンレスは,さびにくく強いことで有名な材料です.今回の軸は,屋外での使用という条件とアルミだと曲がる可能性があったので,ステンレスを材料として選びました.しかし,ステンレスは加工がしにくい材料でもあります.初めてやるステンレスの加工は大変で,普段加工しているアルミの加工性の良さをひしひしと感じました.
そんなこんなで材料がそろいました.
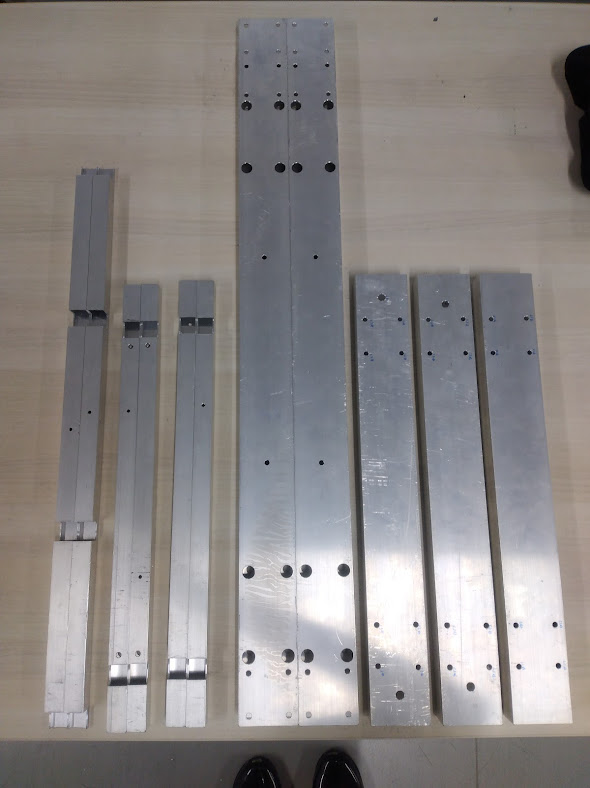
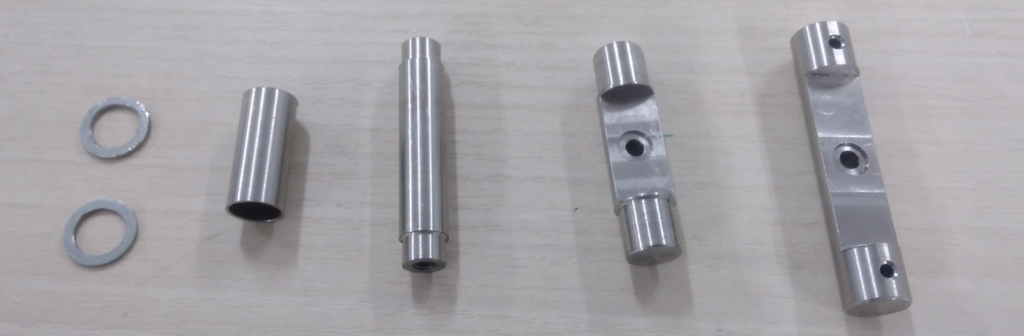
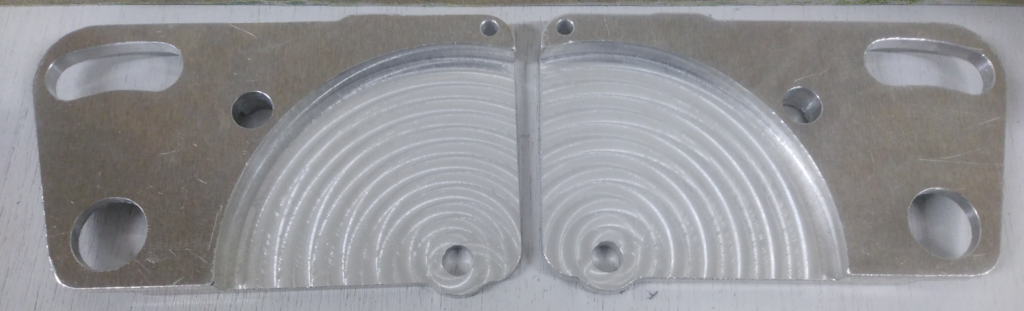
(本当はもう少し部品つくったのですが,写真を撮り忘れていました…)
台車のフレームとキャスターを組み上げて,フレームにキャスター(×4)をくっつけます↓.
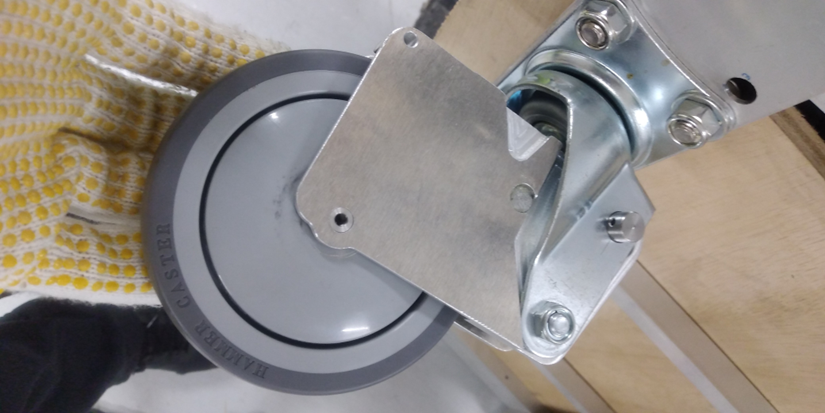
除振台車2号機の完成した姿は…
「完成した2号機はどんな見た目なの??」「動かしてみたらどうだった??」と気になる方もいらっしゃると思いますが,長くなりそうなので,また次のブログ「除振台車を作ってみた~完成・評価編~」に書こうと思います.
果たして,苦労して作り上げた台車はどんな見た目なのか…本当に「除振」してくれたのか…その結果やいかに!